Методите за нанасяне на покритие на фоторезист обикновено се разделят на центрофугиране, покритие с потапяне и ролково покритие, сред които центрофугирането е най-често използваното. Чрез центрофугиране, фоторезистът се накапва върху субстрата и субстратът може да се върти с висока скорост, за да се получи филм от фоторезист. След това може да се получи твърд филм чрез нагряване на котлон. Спиновото покритие е подходящо за покриване от ултратънки филми (около 20nm) до дебели филми от около 100um. Характеристиките му са добра еднородност, еднаква дебелина на филма между пластините, малко дефекти и т.н., и може да се получи филм с висока производителност на покритие.
Процес на центрофугиране
По време на центрофугиране, основната скорост на въртене на субстрата определя дебелината на филма на фоторезиста. Връзката между скоростта на въртене и дебелината на филма е следната:
Спин=kTn
Във формулата Spin е скоростта на въртене; T е дебелината на филма; k и n са константи.
Фактори, влияещи върху процеса на центрофугиране
Въпреки че дебелината на филма се определя от основната скорост на въртене, тя също е свързана със стайната температура, влажността, вискозитета на фоторезиста и вида на фоторезиста. Сравнението на различни типове криви на покритие от фоторезист е показано на фигура 1.
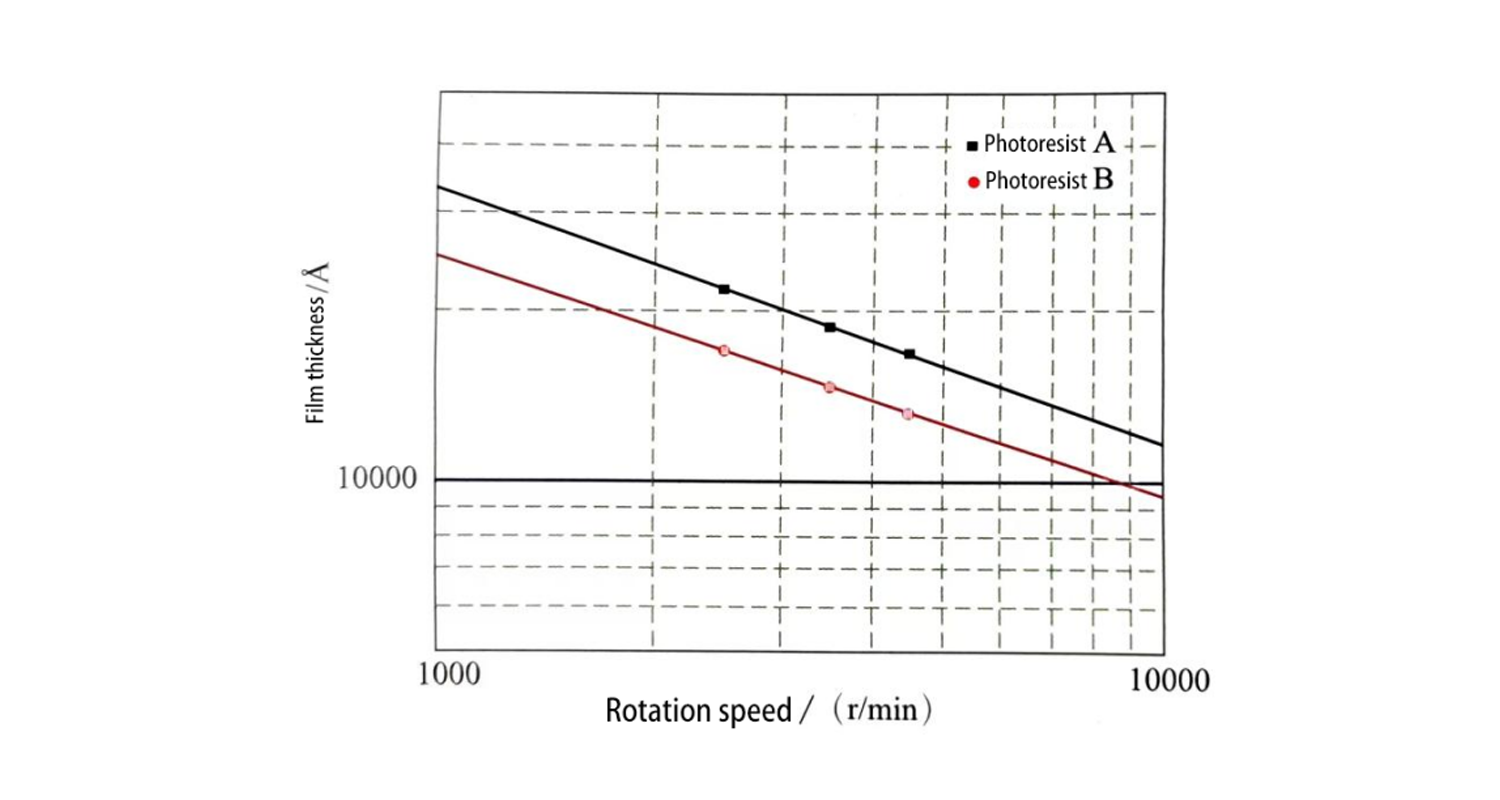
Фигура 1: Сравнение на различни видове криви на покритие от фоторезист
Влиянието на времето на основно въртене
Колкото по-кратко е времето за основно въртене, толкова по-дебела е дебелината на филма. Когато основното време на въртене се увеличи, толкова по-тънък става филмът. Когато превиши 20 s, дебелината на филма остава почти непроменена. Следователно основното време на въртене обикновено се избира да бъде повече от 20 секунди. Връзката между основното време на въртене и дебелината на филма е показана на фигура 2.
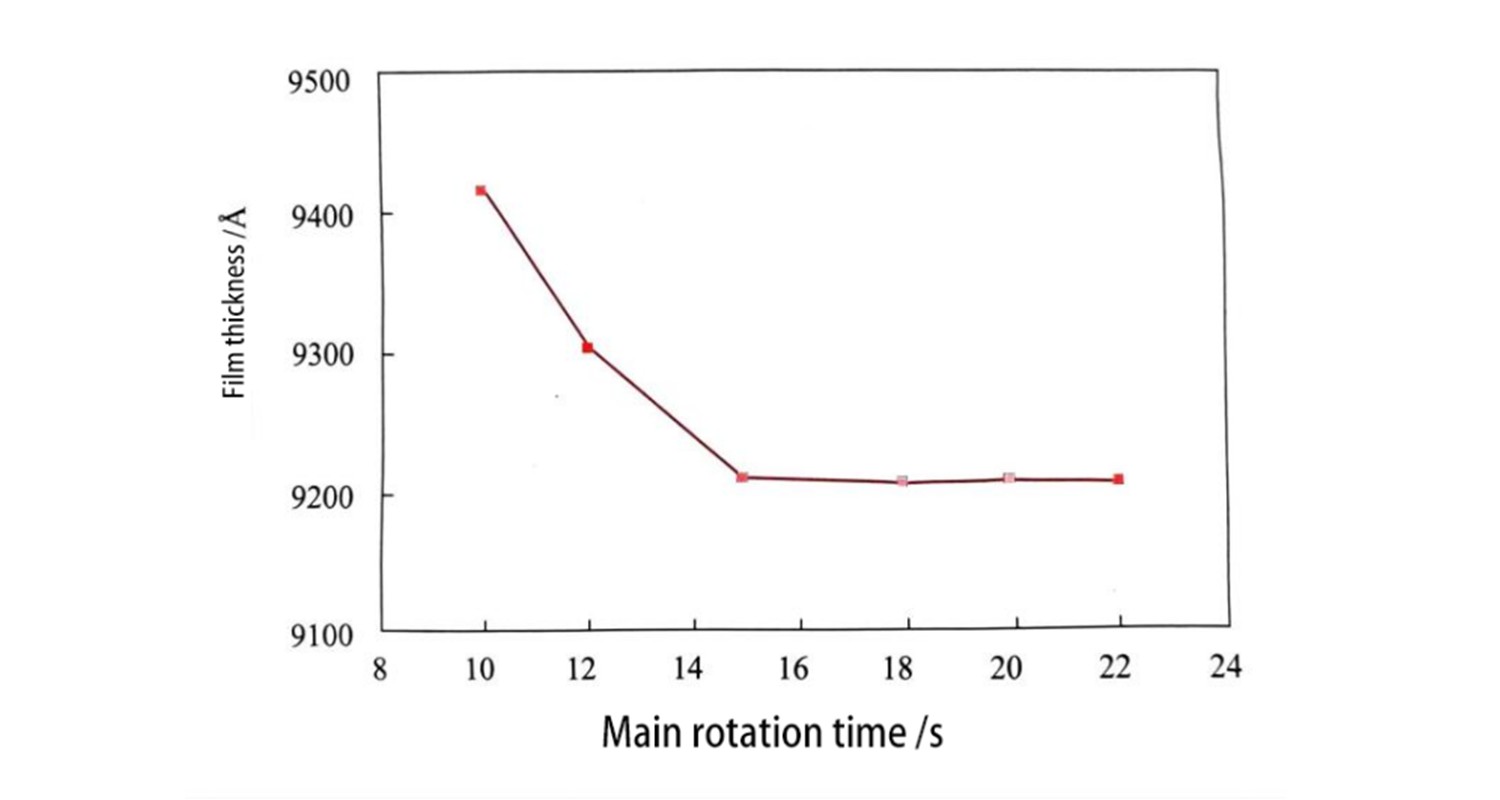
Фигура 2: Връзка между времето на основно въртене и дебелината на филма
Когато фоторезистът се накапе върху субстрата, дори ако последващата основна скорост на въртене е същата, скоростта на въртене на субстрата по време на накапването ще повлияе на крайната дебелина на филма. Дебелината на фоторезистния филм се увеличава с увеличаване на скоростта на въртене на субстрата по време на накапване, което се дължи на влиянието на изпарението на разтворителя, когато фоторезистът се разгъва след накапване. Фигура 3 показва връзката между дебелината на филма и основната скорост на въртене при различни скорости на въртене на субстрата по време на капенето на фоторезиста. От фигурата може да се види, че с увеличаване на скоростта на въртене на капещия субстрат, дебелината на филма се променя по-бързо и разликата е по-очевидна в зоната с по-ниска основна скорост на въртене.
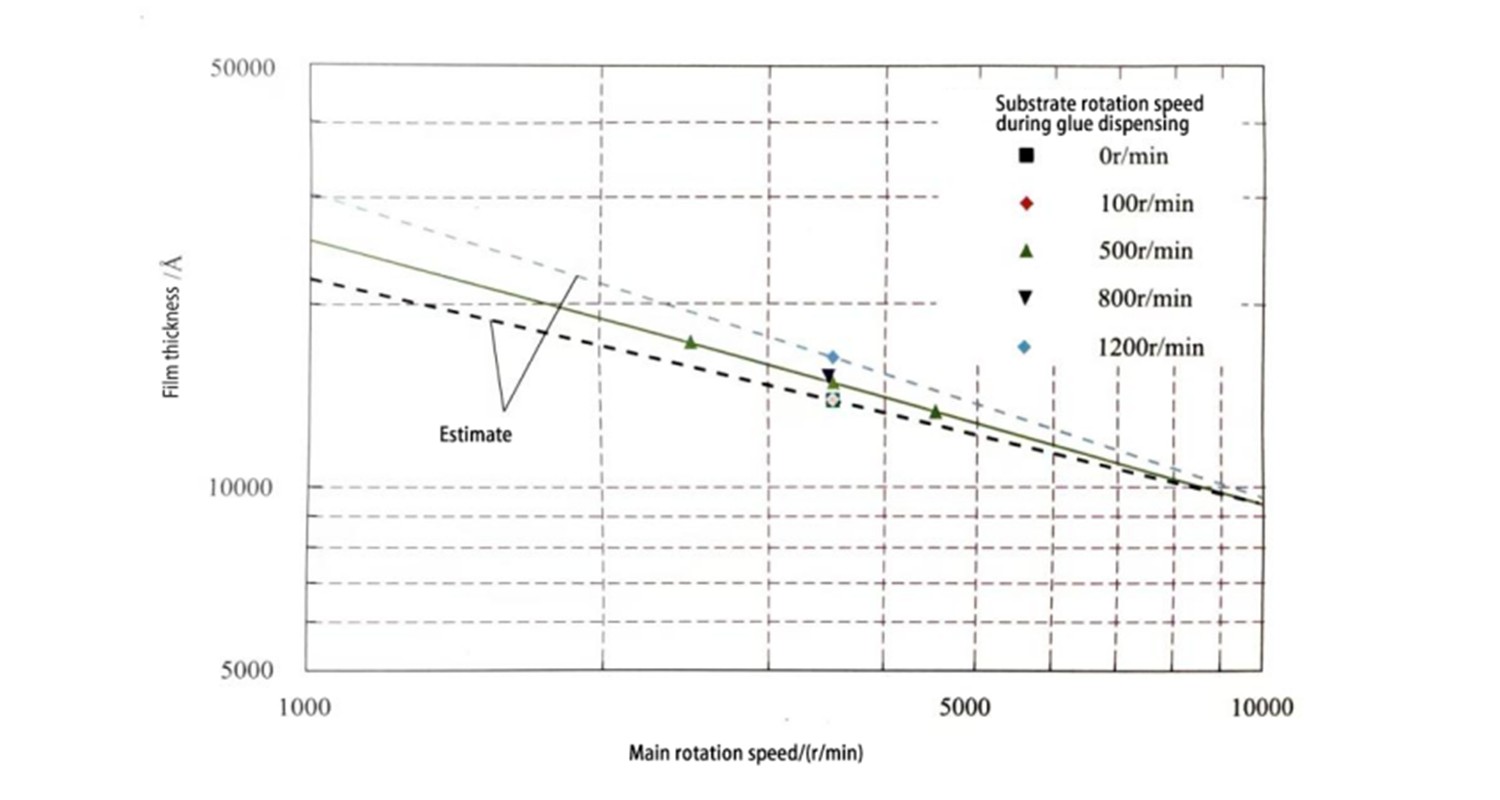
Фигура 3: Връзка между дебелината на филма и основната скорост на въртене при различни скорости на въртене на субстрата по време на дозиране на фоторезист
Влияние на влажността по време на нанасяне на покритие
Когато влажността намалява, дебелината на филма се увеличава, тъй като намаляването на влажността насърчава изпарението на разтворителя. Разпределението на дебелината на филма обаче не се променя значително. Фигура 4 показва връзката между влажността и разпределението на дебелината на филма по време на нанасяне на покритие.
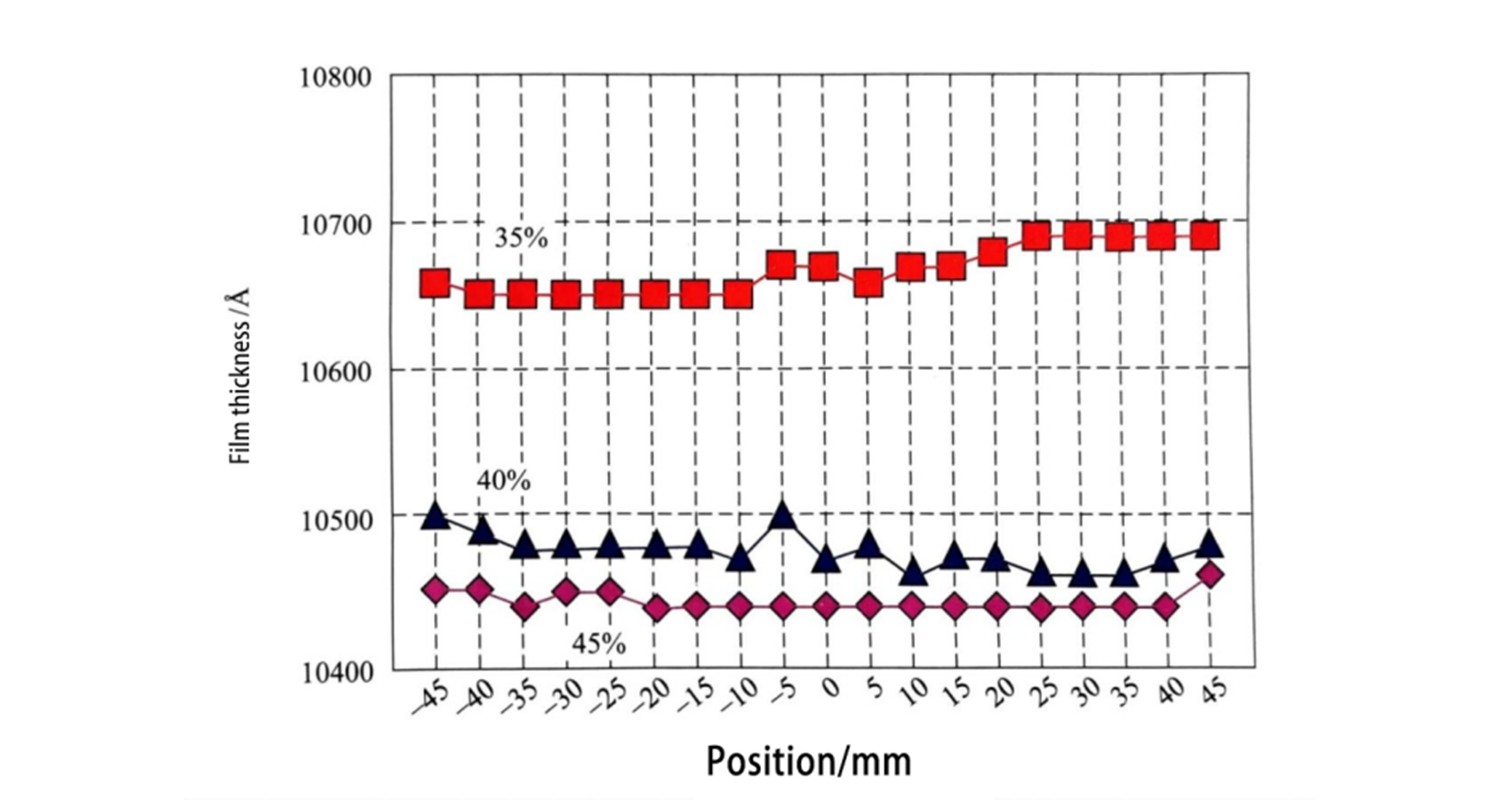
Фигура 4: Връзка между влажността и разпределението на дебелината на филма по време на нанасяне на покритие
Влияние на температурата по време на нанасяне на покритие
Когато вътрешната температура се повиши, дебелината на филма се увеличава. Може да се види от фигура 5, че разпределението на дебелината на фоторезистния филм се променя от изпъкнало на вдлъбнато. Кривата на фигурата също показва, че най-високата равномерност се получава, когато вътрешната температура е 26°C и температурата на фоторезиста е 21°C.
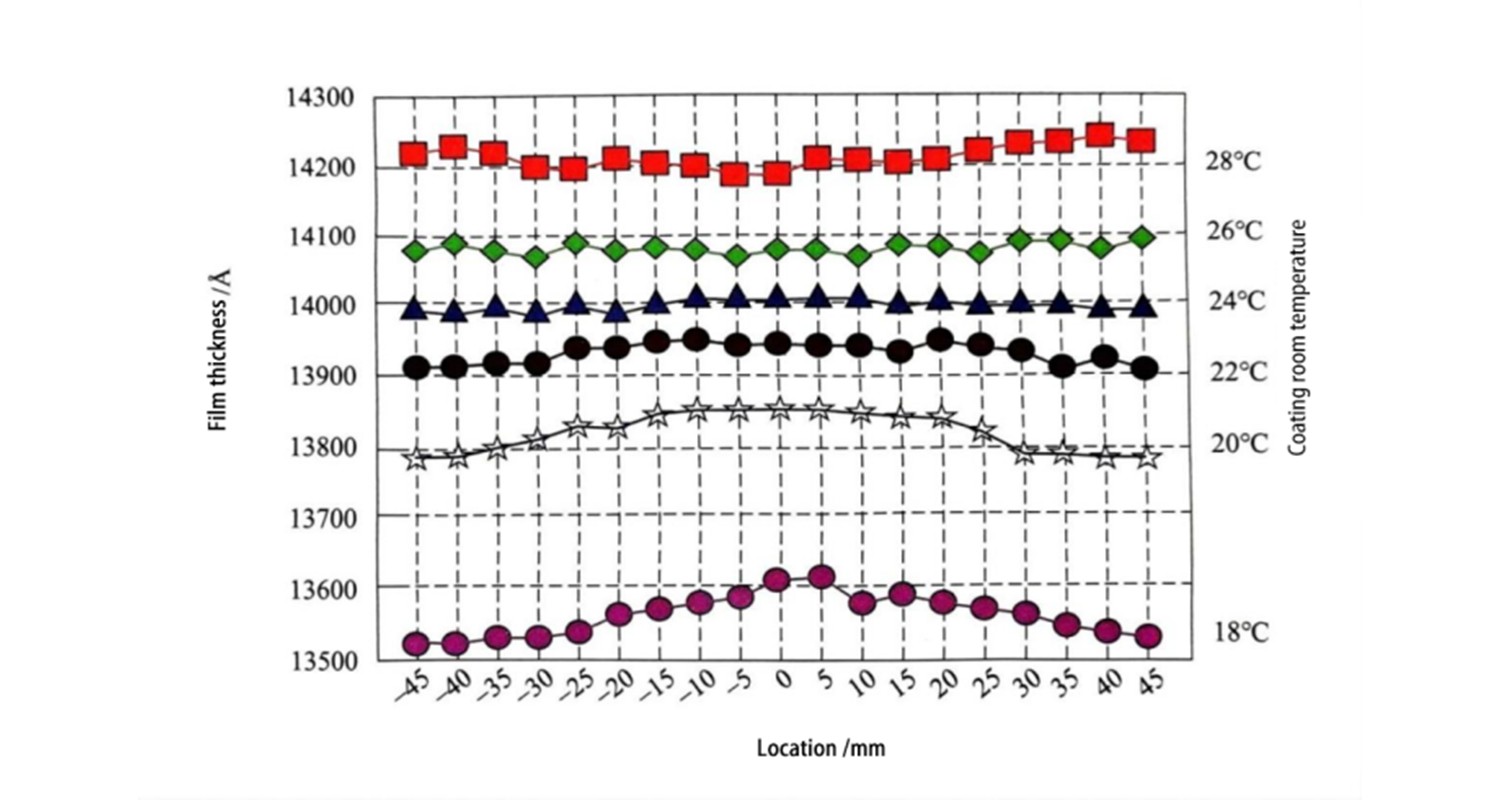
Фигура 5: Връзка между температурата и разпределението на дебелината на филма по време на нанасяне на покритие
Влияние на скоростта на изпускане по време на нанасяне на покритие
Фигура 6 показва връзката между скоростта на изпускане и разпределението на дебелината на филма. При липса на изгорели газове, това показва, че центърът на вафлата има тенденция да се удебелява. Увеличаването на скоростта на изпускане ще подобри равномерността, но ако се увеличи твърде много, равномерността ще намалее. Вижда се, че има оптимална стойност за скоростта на отработените газове.
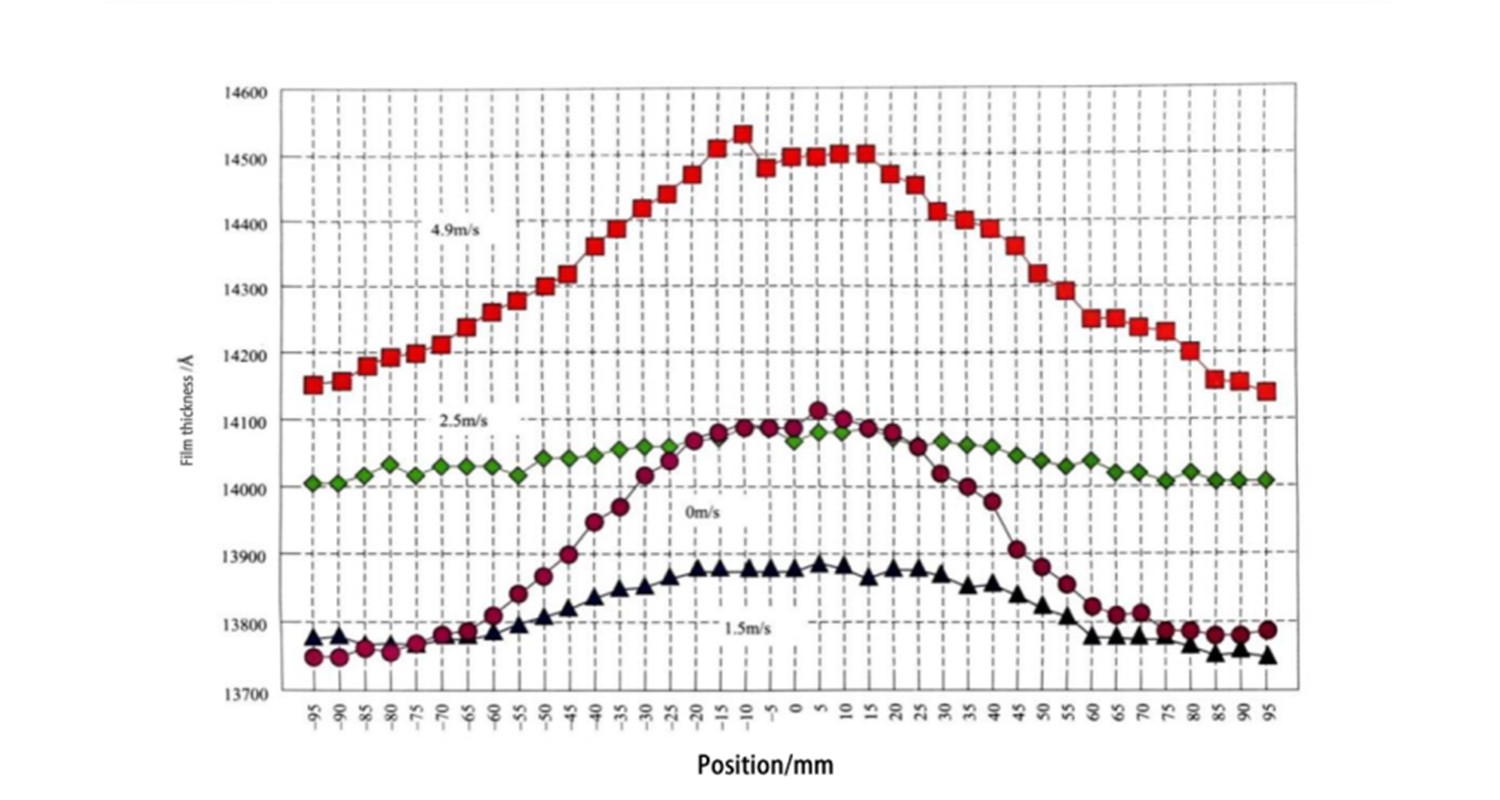
Фигура 6: Връзка между скоростта на изпускане и разпределението на дебелината на филма
Лечение с HMDS
За да се направи фоторезистът по-подходящ за покритие, вафлата трябва да бъде обработена с хексаметилдисилазан (HMDS). Особено когато влагата е прикрепена към повърхността на Si оксидния филм, се образува силанол, който намалява адхезията на фоторезиста. За да се отстрани влагата и да се разложи силанолът, пластината обикновено се нагрява до 100-120°C и се въвежда мъгла HMDS, за да предизвика химическа реакция. Механизмът на реакцията е показан на фигура 7. Чрез третиране с HMDS хидрофилната повърхност с малък контактен ъгъл се превръща в хидрофобна повърхност с голям контактен ъгъл. Нагряването на пластината може да постигне по-висока адхезия на фоторезиста.
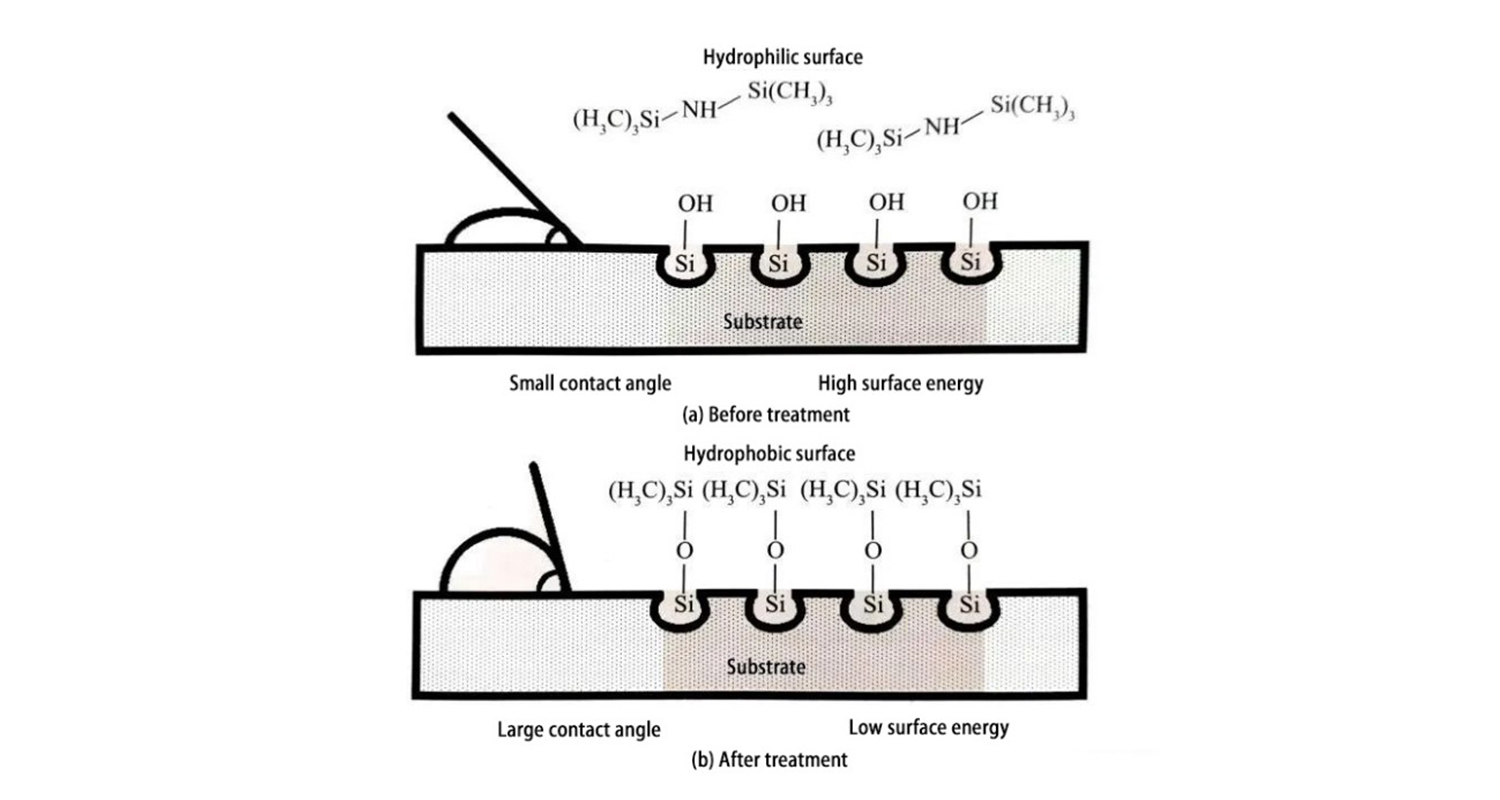
Фигура 7: HMDS реакционен механизъм
Ефектът от лечението с HMDS може да се наблюдава чрез измерване на контактния ъгъл. Фигура 8 показва връзката между времето за обработка с HMDS и контактния ъгъл (температура на обработка 110°C). Субстратът е Si, времето за лечение с HMDS е по-голямо от 1 минута, контактният ъгъл е по-голям от 80 ° и ефектът от лечението е стабилен. Фигура 9 показва връзката между температурата на обработка с HMDS и контактния ъгъл (време на обработка 60 s). Когато температурата надвиши 120 ℃, контактният ъгъл намалява, което показва, че HMDS се разлага поради топлина. Следователно лечението с HMDS обикновено се извършва при 100-110 ℃.
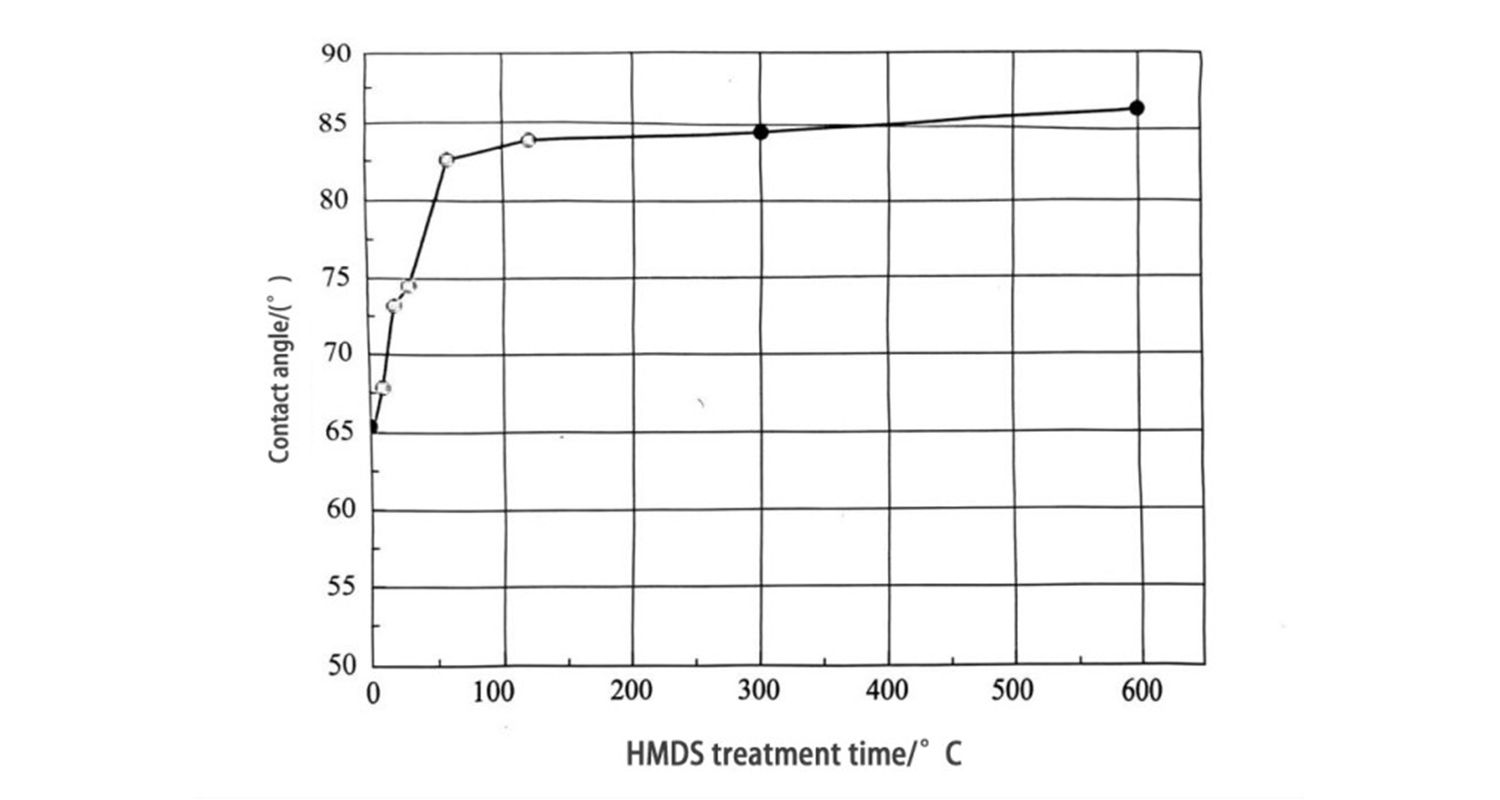
Фигура 8: Връзка между времето за лечение с HMDS
и контактен ъгъл (температура на обработка 110 ℃)
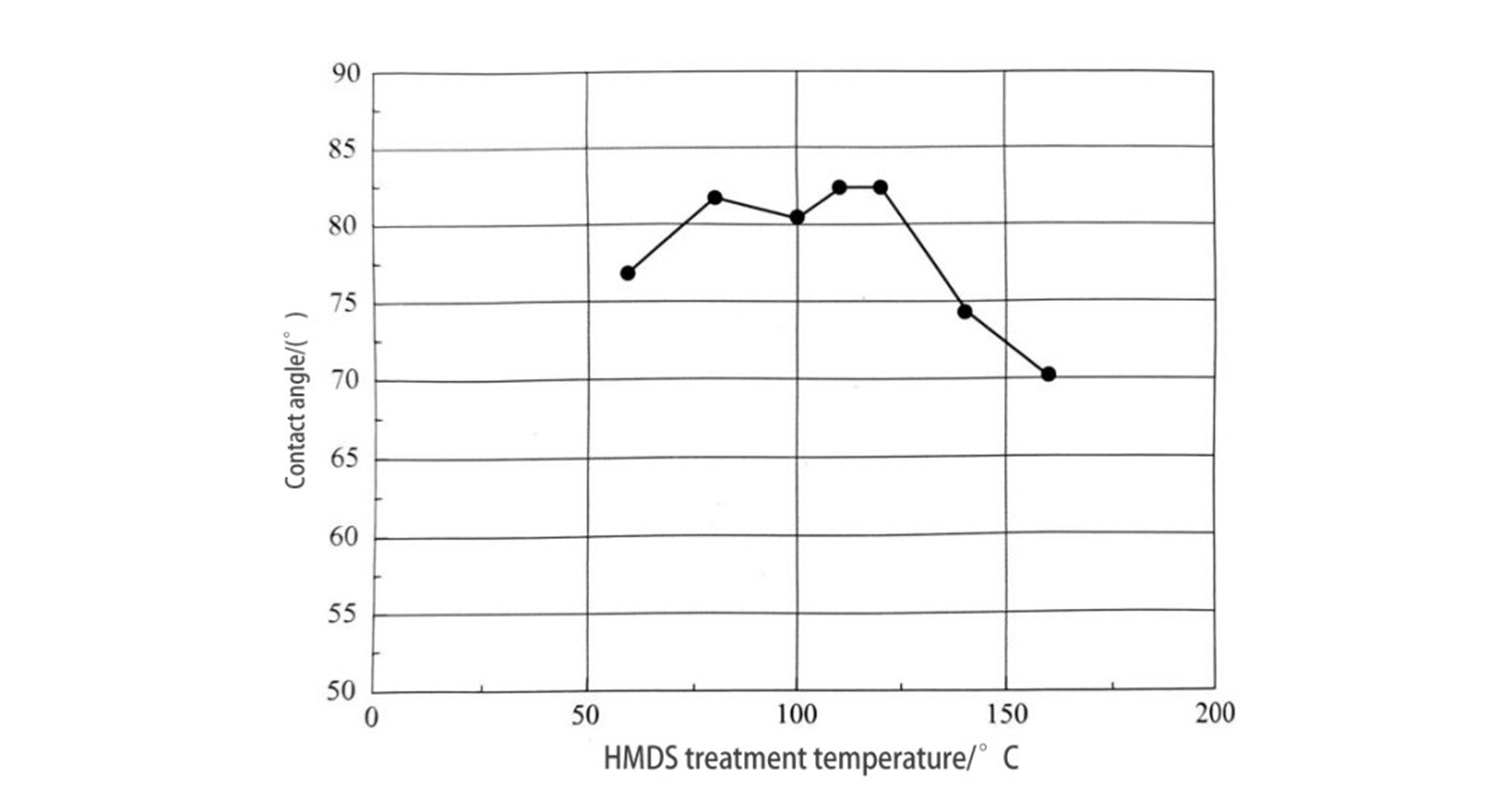
Фигура 9: Връзка между температурата на обработка с HMDS и контактния ъгъл (време на обработка 60 s)
Обработката с HMDS се извършва върху силиконов субстрат с оксиден филм, за да се образува модел на фоторезист. След това оксидният филм се гравира с флуороводородна киселина с добавен буфер и се установява, че след третиране с HMDS фоторезистът може да бъде предпазен от падане. Фигура 10 показва ефекта от лечението с HMDS (размерът на шаблона е 1 um).
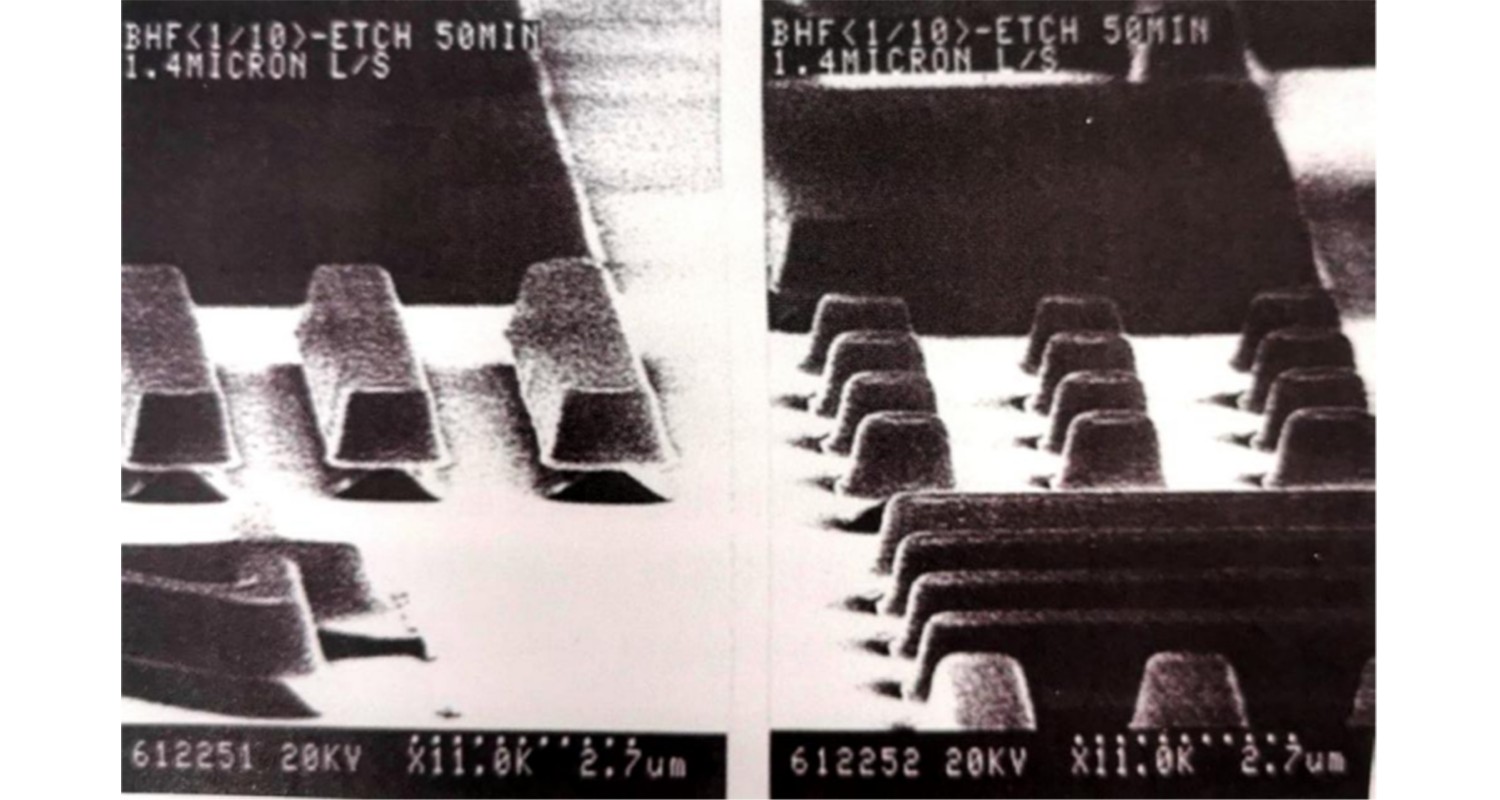
Фигура 10: Ефект от лечението с HMDS (размерът на шаблона е 1 um)
Предварително изпичане
При същата скорост на въртене, колкото по-висока е температурата на предварително изпичане, толкова по-малка е дебелината на филма, което показва, че колкото по-висока е температурата на предварително изпичане, толкова повече разтворител се изпарява, което води до по-тънка дебелина на филма. Фигура 11 показва връзката между температурата на предварително изпичане и параметъра A на Dill. Параметърът А показва концентрацията на фоточувствителния агент. Както може да се види от фигурата, когато температурата на предварително изпичане се повиши до над 140°C, параметърът A намалява, което показва, че фоточувствителният агент се разлага при температура, по-висока от тази. Фигура 12 показва спектралната пропускливост при различни температури преди печене. При 160°C и 180°C може да се наблюдава увеличение на пропускливостта в диапазона на дължината на вълната от 300-500nm. Това потвърждава, че фоточувствителният агент се изпича и разлага при високи температури. Температурата на предварително изпичане има оптимална стойност, която се определя от светлинните характеристики и чувствителността.
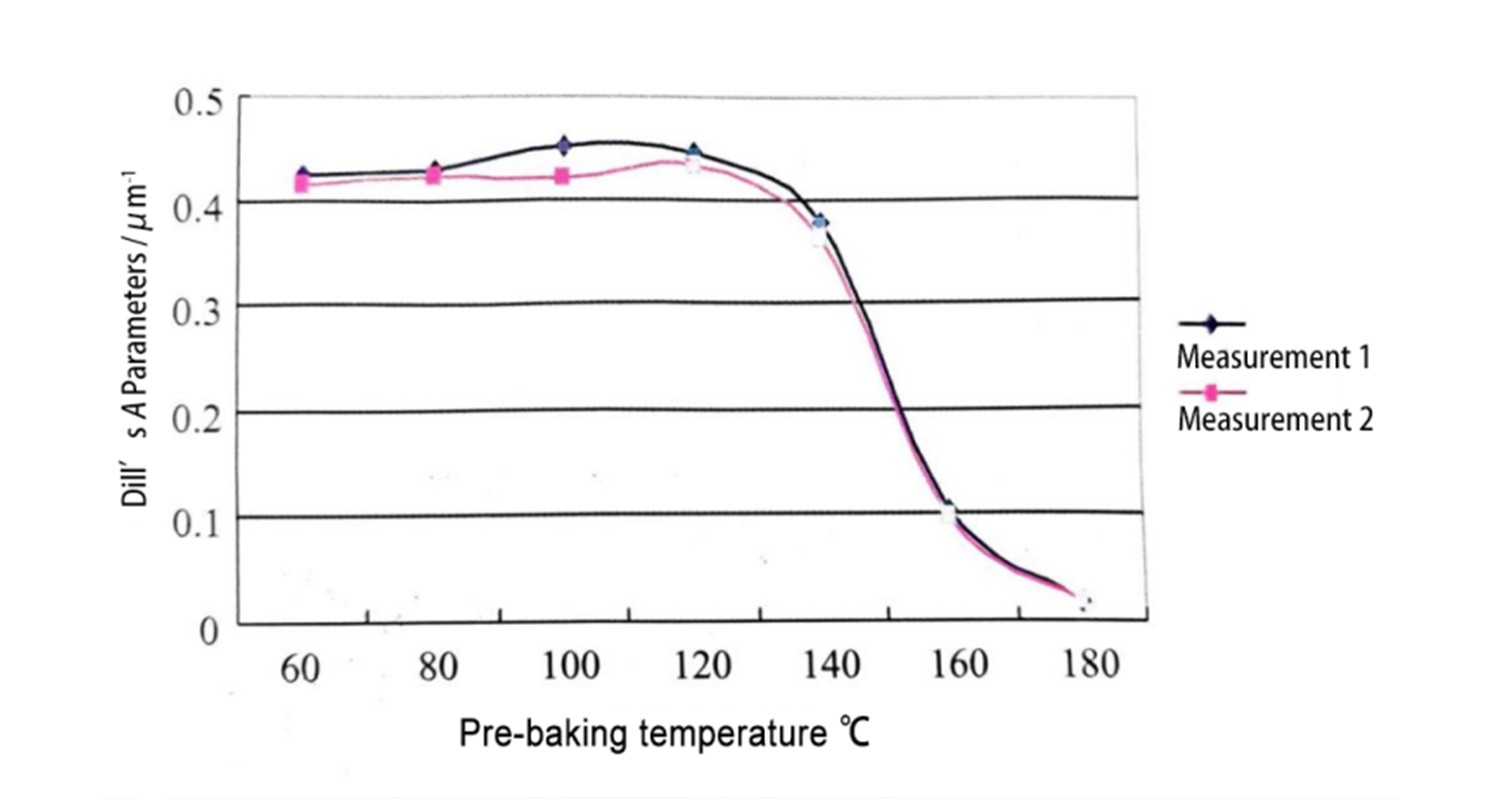
Фигура 11: Връзка между температурата преди печене и параметъра A на Dill
(измерена стойност на OFPR-800/2)
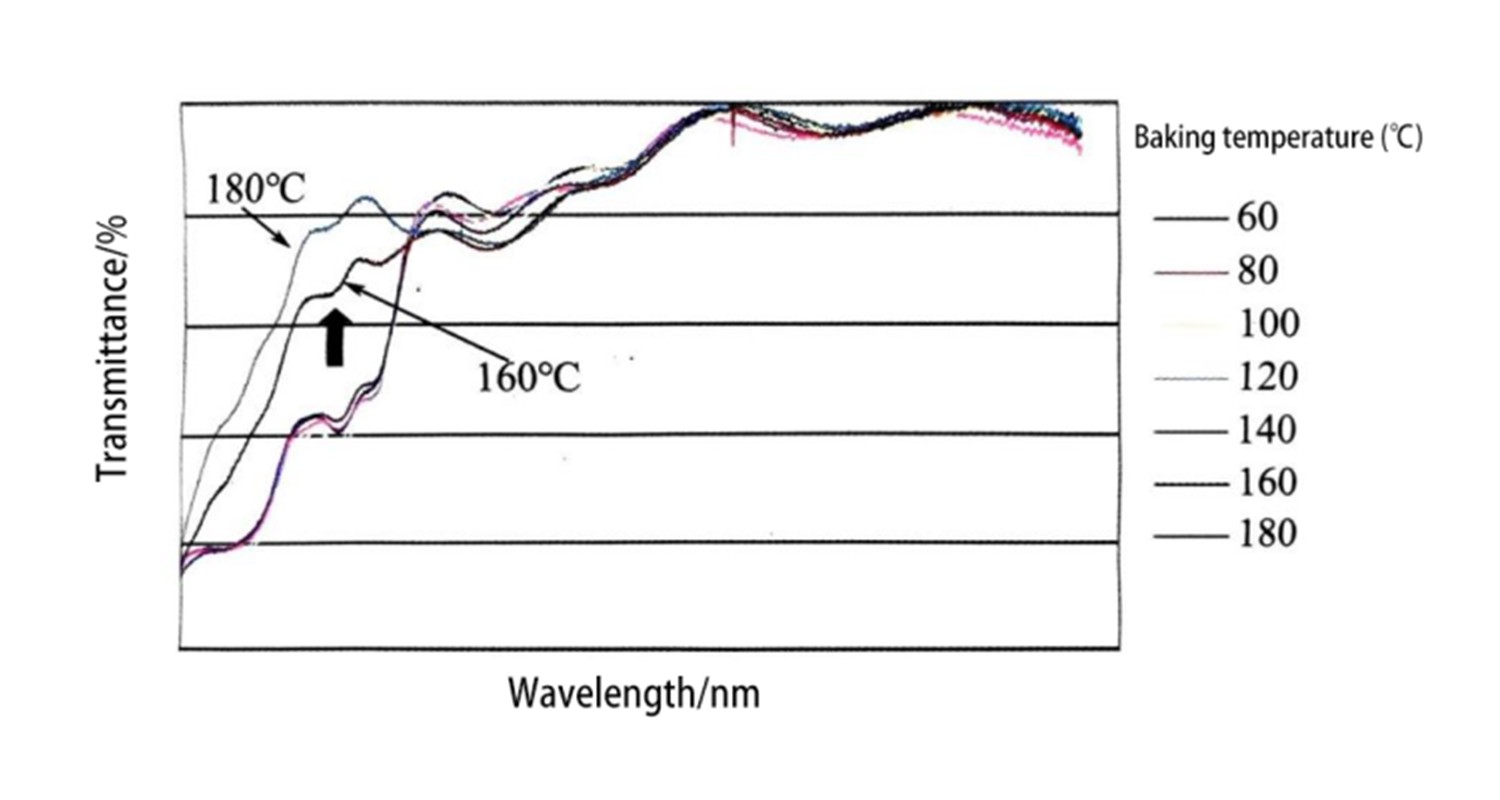
Фигура 12: Спектрална пропускливост при различни температури преди печене
(OFPR-800, 1um дебелина на филма)
Накратко, методът на центрофугиране има уникални предимства като прецизен контрол на дебелината на филма, висока производителност на разходите, меки условия на процеса и проста работа, така че има значителни ефекти за намаляване на замърсяването, пестене на енергия и подобряване на ефективността на разходите. През последните години центрофугирането привлича все повече внимание и приложението му постепенно се разпространи в различни области.
Време на публикуване: 27 ноември 2024 г