Керамиката от силициев нитрид (Si₃N₄), като усъвършенствана структурна керамика, притежава отлични свойства като устойчивост на висока температура, висока якост, висока якост, висока твърдост, устойчивост на пълзене, устойчивост на окисление и устойчивост на износване. Освен това те предлагат добра устойчивост на термичен удар, диелектрични свойства, висока топлопроводимост и отлично предаване на високочестотни електромагнитни вълни. Тези изключителни всеобхватни свойства ги правят широко използвани в сложни структурни компоненти, особено в космическото пространство и други високотехнологични области.
Въпреки това, Si3N4, като съединение със силни ковалентни връзки, има стабилна структура, която прави синтероването до висока плътност трудно само чрез дифузия в твърдо състояние. За насърчаване на синтероването се добавят помощни средства за синтероване, като метални оксиди (MgO, CaO, Al₂O3) и редкоземни оксиди (Yb₂O3, Y₂O₃, Lu₂O₃, CeO₂), за да се улесни уплътняването чрез механизъм за синтероване в течна фаза.
Понастоящем глобалната технология на полупроводниковите устройства напредва към по-високи напрежения, по-големи токове и по-висока плътност на мощността. Изследванията на методите за производство на Si₃N4 керамика са обширни. Тази статия въвежда процеси на синтероване, които ефективно подобряват плътността и цялостните механични свойства на керамиката от силициев нитрид.
Обичайни методи за синтероване на Si₃N₄ керамика
Сравнение на производителността на Si₃N₄ керамика, получена чрез различни методи на синтероване
1. Реактивно синтероване (RS):Реактивното синтероване е първият метод, използван за промишлено приготвяне на Si₃N4 керамика. Той е прост, рентабилен и способен да формира сложни форми. Той обаче има дълъг производствен цикъл, който не е благоприятен за производство в промишлен мащаб.
2. Агломериране без налягане (PLS):Това е най-основният и прост процес на синтероване. Той обаче изисква висококачествени Si₃N₄ суровини и често води до керамика с по-ниска плътност, значително свиване и склонност към напукване или деформиране.
3. Горещо пресоване (HP):Прилагането на едноосно механично налягане увеличава движещата сила за синтероване, което позволява да се произвежда плътна керамика при температури със 100-200°C по-ниски от тези, използвани при синтероване без налягане. Този метод обикновено се използва за производство на относително проста керамика с форма на блок, но е трудно да се изпълнят изискванията за дебелина и форма на субстратните материали.
4. Искрово плазмено синтероване (SPS):SPS се характеризира с бързо синтероване, усъвършенстване на зърното и намалени температури на синтероване. Въпреки това, SPS изисква значителни инвестиции в оборудване и подготовката на Si₃N4 керамика с висока топлопроводимост чрез SPS е все още в експериментален етап и все още не е индустриализирана.
5. Агломериране под налягане (GPS):Чрез прилагане на газово налягане, този метод възпрепятства разлагането на керамиката и загубата на тегло при високи температури. По-лесно е да се произвежда керамика с висока плътност и позволява серийно производство. Едноетапният процес на синтероване под газово налягане обаче се бори да произведе структурни компоненти с еднакъв вътрешен и външен цвят и структура. Използването на двуетапен или многоетапен процес на синтероване може значително да намали съдържанието на кислород между гранулите, да подобри топлопроводимостта и да подобри цялостните свойства.
Въпреки това, високата температура на синтероване при двуетапно синтероване под налягане на газ е накарала предишни изследвания да се съсредоточат главно върху подготовката на Si₃N4 керамични субстрати с висока топлопроводимост и якост на огъване при стайна температура. Изследванията на Si₃N4 керамика с всеобхватни механични свойства и механични свойства при висока температура са сравнително ограничени.
Двуетапен метод на синтероване под налягане на газ за Si₃N4
Yang Zhou и колеги от Технологичния университет в Чунцин са използвали система за подпомагане на синтероването от 5 тегл.% Yb₂O3 + 5 тегл.% Al2O3, за да приготвят Si3N4 керамика, използвайки както едноетапни, така и двуетапни процеси на синтероване под газово налягане при 1800°C. Si₃N4 керамиката, произведена чрез двуетапния процес на синтероване, има по-висока плътност и по-добри цялостни механични свойства. По-долу са обобщени ефектите от едноетапни и двуетапни процеси на синтероване под газово налягане върху микроструктурата и механичните свойства на Si₃N4 керамичните компоненти.
Плътност Процесът на уплътняване на Si₃N4 обикновено включва три етапа, с припокриване между етапите. Първият етап, пренареждане на частиците, и вторият етап, разтваряне-утаяване, са най-критичните етапи за уплътняване. Достатъчното време за реакция в тези етапи значително подобрява плътността на пробата. Когато температурата на предварително синтероване за двуетапния процес на синтероване е настроена на 1600°C, зърната β-Si₃N4 образуват рамка и създават затворени пори. След предварително синтероване по-нататъшното нагряване при висока температура и налягане на азот насърчава потока на течната фаза и пълненето, което спомага за елиминирането на затворените пори, като допълнително подобрява плътността на Si₃N₄ керамиката. Следователно, пробите, произведени чрез процеса на двуетапно синтероване, показват по-висока плътност и относителна плътност от тези, произведени чрез едноетапно синтероване.
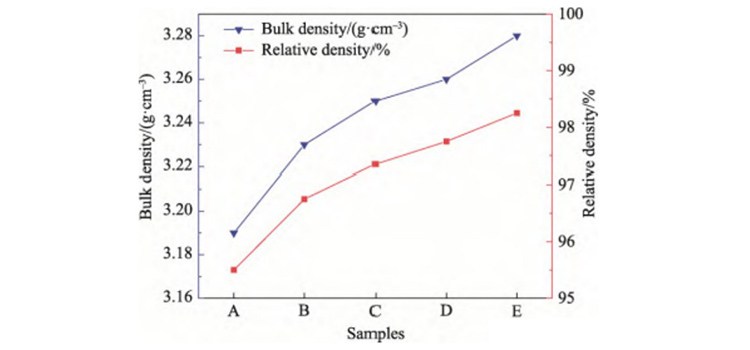
Фаза и микроструктура По време на едноетапно синтероване наличното време за пренареждане на частиците и дифузия по границите на зърната е ограничено. В двуетапния процес на синтероване, първият етап се провежда при ниска температура и ниско налягане на газа, което удължава времето за пренареждане на частиците и води до по-големи зърна. След това температурата се повишава до високотемпературния етап, където зърната продължават да растат чрез процеса на узряване на Ostwald, като се получава Si₃N₄ керамика с висока плътност.
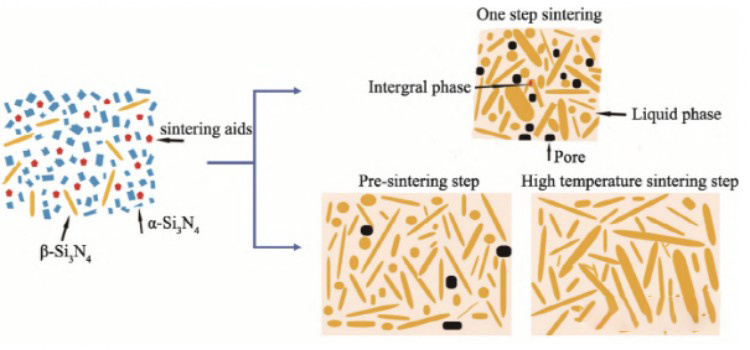
Механични свойства Размекването на междугранулираната фаза при високи температури е основната причина за намалената якост. При едноетапно синтероване необичайният растеж на зърната създава малки пори между зърната, което предотвратява значително подобряване на якостта при висока температура. Въпреки това, в двуетапния процес на синтероване, стъклената фаза, равномерно разпределена в границите на зърната, и зърната с еднакъв размер повишават междукристалната якост, което води до по-висока якост на огъване при висока температура.
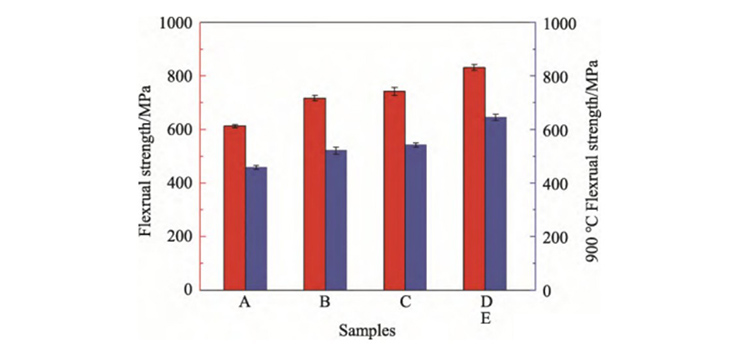
В заключение, продължителното задържане по време на едноетапно синтероване може ефективно да намали вътрешната порьозност и да постигне равномерен вътрешен цвят и структура, но може да доведе до необичаен растеж на зърната, което влошава някои механични свойства. Чрез използване на двуетапен процес на синтероване - използване на нискотемпературно предварително синтероване за удължаване на времето за пренареждане на частиците и задържане при висока температура за насърчаване на равномерен растеж на зърната - Si₃N4 керамика с относителна плътност от 98,25%, равномерна микроструктура и отлични цялостни механични свойства може да се подготви успешно.
Име | Субстрат | Състав на епитаксиален слой | Епитаксиален процес | Епитаксиална среда |
Силициев хомоепитаксиален | Si | Si | Парна фазова епитаксия (VPE) | SiCl4+H2 |
Силициев хетероепитаксиален | Сапфир или шпинел | Si | Парна фазова епитаксия (VPE) | SiH4+H2 |
GaAs хомоепитаксиален | GaAs | GaAs GaAs | Парна фазова епитаксия (VPE) | AsCl3+Ga+H2 (Ar) |
GaAs | GaAs GaAs | Молекулярно-лъчева епитаксия (MBE) | Ga+As | |
GaAs хетероепитаксиален | GaAs GaAs | GaAlAs/GaAs/GaAlAs | Епитаксия в течна фаза (LPE) Парна фаза (VPE) | Ga+Al+CaAs+ H2 Ga+AsH3+PH3+CH1+H2 |
GaP хомоепитаксиален | GaP | GaP(GaP;N) | Епитаксия в течна фаза (LPE) Епитаксия в течна фаза (LPE) | Ga+GaP+H2+(NH3) Ga+GaAs+GaP+NH3 |
Суперрешетка | GaAs | GaAlAs/GaAs (цикъл) | Молекулярно-лъчева епитаксия (MBE) MOCVD | Ca, As, Al GaR3+AlR3+AsH3+H2 |
InP хомоепитаксиален | InP | InP | Парна фазова епитаксия (VPE) Епитаксия в течна фаза (LPE) | PCl3+In+H2 In+InAs+GaAs+InP+H₂ |
Si/GaAs епитаксия | Si | GaAs | Молекулярно-лъчева епитаксия (MBE) MOGVD | Ga、As GaR3+AsH3+H2 |
Време на публикуване: 24 декември 2024 г